Robots Offshore: Spot, ANYmal, and more
- Sarah Whiteford
- Aug 20, 2021
- 5 min read
Over the last couple of years, offshore robotics has graduated from “it’s coming soon” to a reality. Legged, tracked, and even wheeled robots are walking and scooting around facilities, performing inspections. These tasks are either dangerous for humans or just plain time-consuming and repetitive. Robots can use sensors to see things we can’t, like infrared and emissions. You’ve probably seen at least one of these robots on YouTube or on the news walking, working, or even dancing. It’s Fun Fact Friday, let’s take a look at some of the ground-based robots currently in use offshore and onshore, making work easier and safer. Stay tuned, we’ll cover aerial and underwater robots in future articles.
Taurob

“Two Taurob Inspectors, Charles and Eddie, are on a 12-month trial at Shetland Gas Plant in Scotland. Photos from TotalEnergies.” Photo from Offshore Engineer.
TotalEnergies developed the Argos (Autonomous Robots for Gas and Oil Sites) challenge that ran from 2014 to 2017 with the goal of developing robots for unattended facilities, and since then has been working to further develop the technology. The result is the Taurob Inspector, “a tracked vehicle able to travel around a platform to collect various data (video, infrared, sound, remote gas detection, etc.)” according to Offshore Engineer. August of 2020 was the first time a Taurob Inspector was taken offshore for testing, revealing several areas for improvement: it would need the ability to open doors and some of the grated and non-slip floorings destroyed the tracks within weeks. Shortly after in November, Charles and Edward, two Taurob Inspectors went to TotalEnergies for a 12 month trial run by the staff. They are operating in a MEG, or gas dehydration unit, doing their rounds autonomously. Matthias Biegl, co-founder of Taurob, said it’s a big step to hand over the robots to operators without the company being there. More manipulation functions are planned, such as the ability to open and close valves or change filter cartridges. Additional work may even include changeable arms and sensors for different functions like measuring gas content, giving any robot the ability to do specialized tasks.
Video of the Taruob Inspector. Video from Taurob on YouTube.
ANYmal
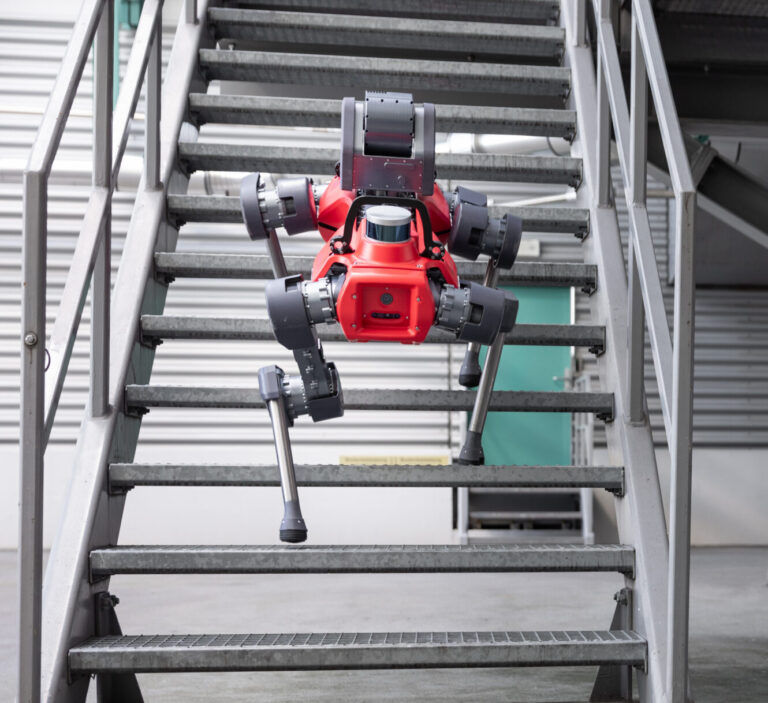
ANYmal walking down stairs. Image from ANYbotics.
ANYbotics ANYmal uses a very different, but more familiar system of movement: legs. ANYmal is equipped with four legs that allow it to walk up and down stairs, over obstacles, under overhangs, tackle slopes, and even navigate across gaps. In addition to great mobility, sensors onboard can read gauges, record audio, and do thermal imaging. It can also 3D map its surroundings to learn more about the space it operates in and navigate better. ANYmal recharges itself at charging stations that can be set up in a central location or along predetermined routes. Petronas took an ANYmal C offshore for three weeks for testing on a hydrocarbon-free platform. According to ANYmal and Offshore Engineer, the robots are IP67 rated, but not yet rated for hazardous environments, which is why initial testing was in a hydrocarbon-free environment. It has already done visual inspections, gauge reading, thermal imaging, audio, and mapped four floors of the facility. It did well on narrow, steep stairs, and had no problems with wind. The video below shows an overview of what ANYmal can do.
Video overview of ANYmal. Video from ANYbotics on YouTube.
Spot

Spot. Image from Boston Dynamics.
Boston Dynamics Spot is a similar quadruped design with four legs and a dog-like appearance. You may recognize Spot from viral video dance numbers or many other times Spot has been in the news. If you’re wondering how they perform those coordinated dance numbers: lots of programming and staying balanced by sending commands 400 times per second. They can be equipped for visual inspection, gauge reading, thermal sensing, and process visuals for leak detection. Spot can complete laser scanning to produce a digital twin of the work environment to more quickly identify areas of rework. Noise anomalies, gas detection, radiation detection, and even search and alert in hazardous environments and disaster areas are all capabilities. It can also be equipped with other optional sensors and equipment like grabbing arms to move objects and open doors. According to Offshore Engineer, Spot has even been equipped with a “precision acoustic sensor to identify non-conformities in offshore machinery, has been risk-assessed and approved for offshore use in non-classified areas”. Spot is already working with bp, Woodside, and other energy companies for offshore inspection work. The video below shows some of the functions it can perform with an arm attachment, it’s quite impressive!
Video of Spot using the new arm attachment. Video from Boston Dynamics on YouTube.
BladeBUG

“BladeBUG is a blade walking inspection robot, focusing on leading edge erosion inspection. Images from ORE Catapult.” Image from Offshore Engineer. *Writer’s note: BladeBUG is not as sinister as it appears above.
Created by a wind turbine engineer, BladeBUG was created to make offshore wind inspections safer. The robot uses a hexapod, or six-legged design with suction devices attached to the end of its legs to grip the blades of wind turbines. It can walk anywhere on a turbine blade and can be operated out of line of sight from humans. As we discussed in a previous Good News Monday, currently humans have to manually inspect every inch of wind turbine blades - a tedious and dangerous job. BladeBUG has the ability to crawl across the structures and inspect bolt integrity ultrasonically with a technology called EchoBolt. Measuring bolt tension in this way also means bolts don’t have to be loosened and tightened to ensure proper torque. BladeBUG is based in the UK, where there will be an estimated 250,000 turbine blades by 2050. That’s 79,000,000 bolts that will need to be inspected. According to the BladeBUG website, the first successful turbine walk was completed in October 2020. We’ve seen more recent news in June 2021 from The Engineer that continued tests like walking an entire blade remotely are going well. Check out the video about BladeBUG below.
Video overview of BladeBUG. Video from UK Research and Innovation on YouTube.
BIKE

BIKE robot. Image from Waygate Technologies.
The BIKE robot was specifically designed to reach places that are difficult for humans to go due to “size constraints, temperature, immersion in liquids or safety reasons”, according to Waygate Technologies, developer of BIKE. It has magnetic wheels allowing it to adhere to the inside or outside surfaces, even operating upside down in pipes, tanks, and other metal areas. Although wheeled, it can navigate stairs and 90 degree corners with sensors to deliver precise information about positioning. It provides inspection information via different modules like a borescope to look into hard to reach areas, as well as an ultrasonic module for thickness measurements, and an advanced inspection camera with 10x zoom. It can also provide 3D mapping and works on coated surfaces with a wheel change. Future upgrades include a remote arm that will hold more tools. BIKE is 10kg and can deploy through a 12” manway for interior operation or operation on outside pipes 15” or larger.
Video of BIKE performing a borescope inspection. Video from Waygate Technologies on YouTube.
We’ve seen robots that walk, drive, and crawl, doing tasks that make work safer for us. It seems like only yesterday autonomous robots walking around doing the time consuming, dangerous tasks was science fiction. We are happy to report that it is now a reality. Some of these robots are still in the testing phases, but others are already being deployed on missions across the world. Robots are especially well suited to offshore, maritime, and the energy industry work where people put their lives on the line every day. Innovations like Taurob Inspector, ANYmal, Spot, BladeBUG, and BIKE are amazing pieces of technology that can keep people safer in their day-to-day activities and prevent problems before they happen with ultrasonic inspections, thermal scanning, and chemical sensing. We look forward to the growth of robotics and the safety and efficiency it brings.
Happy Friday!
Sources:
Commentaires